
v4.0
with
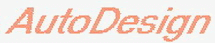
Installation and Operation
Manual:
This on-line manual (TrDsManV28.doc) is included on the CD as a Microsoft Word document file.
Contents
AutoDesign Feature ………………………………………………… 2
Manual Operation (without AutoDesign) ………………………….. 8
Installation ……………………………………………… 17
Parameter Descriptions ……………………………………………. 18
Sample Designs ………………………………………………… 24
Simplified designing with
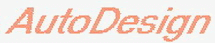
Using the AutoDesign feature, entering minimum design requirements results in a complete transformer design realization .
The following design form is the only form required to be completed:
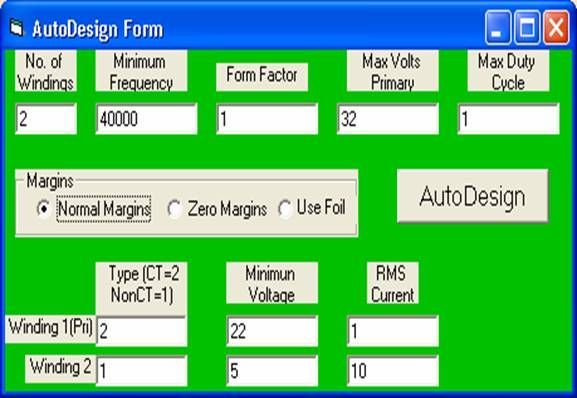
When the AutoDesign form opens, enter the required data as in the following example:
Enter the number of windings (2 to 8)
Enter the minimum operating frequency in Hertz
Enter the form factor (1.11 for a sine wave, 1 for a square wave, etc.)
Enter the maximum expected primary RMS voltage
Enter the duty cycle per unit (Usually 1, but less for pulse width modulation)
The program uses the margins stored with the conductors unless the “Use Foil” or “Zero Margins” radio button is selected. If “Use Foil” is selected, the program calculates foil parameters to fit the core.
Enter the winding type for each of the windings (2 for center-tapped, 1 for not center-tapped)
Enter minimum RMS voltages for each winding
Enter RMS currents for each winding. It is not necessary to enter a current for the first or primary winding - the program calculates it.
Click on AutoDesign. (If “No Dongle Installed” error occurs, see “Installing the Security Device” below.) The program completely designs the transformer and, when finished, displays the output results. The rest of the forms can be displayed by clicking on VIEW then VIEW ALL FORMS:
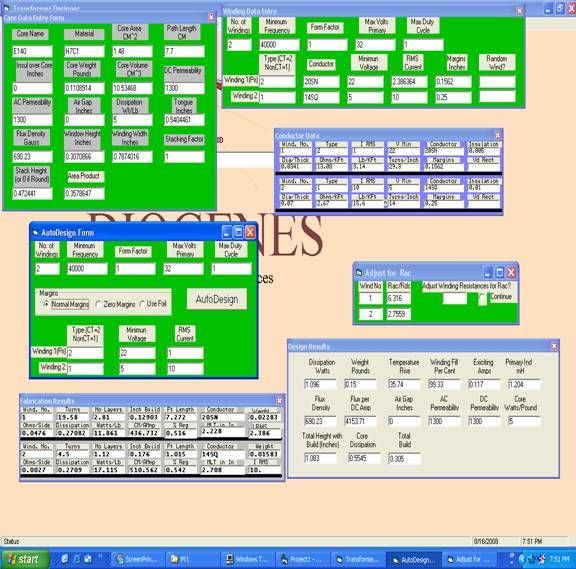
The “AutoDesign” form can be added to the display from the bottom minimized bar. The forms with green background are input forms which, in AutoDesign mode are filled out by the program. The forms with grey background are output forms. The “Design Results” form contains information which the designer can use to determine if the design is optimum. The “Fabrication Results” form contains information the shop can use in the production process.
If this project is saved now, all the input forms and data are saved. When re-opened, “Calculate” from the main menu will reconstitute the output data.
Calculations in AutoDesign mode use the maximum temperature rise of 50 degrees centigrade by default. A different temperature rise can be entered under “Options” on the main menu.
Initially, calculations are made without regard to the increase in resistance due to operating frequency. The “Adjust for Rac” form shows the estimated ratio of AC resistance to DC resistance because of skin depth and proximity effects for each winding.. If it is desirable to recalculate the transformer using the higher AC resistances, answer “Yes” and select “Continue”. Any subsequent calculation will include the AC resistance values. If the AC resistance presents a problem, a recalculation using foil conductor is usually quite effective in reducing the ratio of Rac to Rdc.
Possibly you are not entirely satisfied with the design. Maybe you don’t have an E140 core with H7C1 material on the shelf. Or your shop’s winding practices can’t meet the winding fill requirement (this calculation includes a 5% bulge factor). You can modify anything in the input forms and recalculate manually. Manual design is very flexible, allowing use of any core and any conductor. The Cores Library and Conductor Library can alleviate most of the dog work of entering data.
The output data can be selectively printed in two collections:
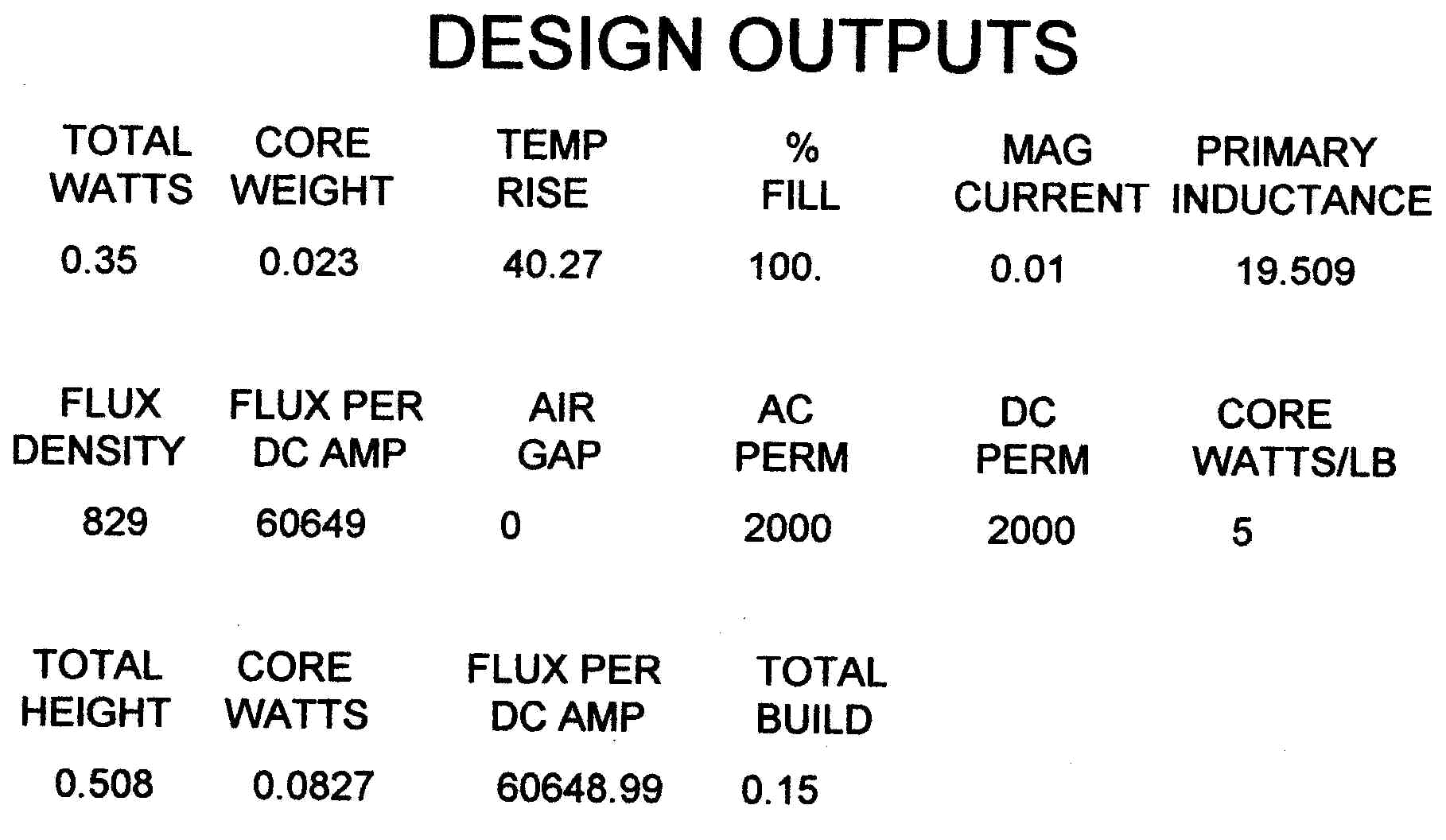
The Design Outputs printout contains data useful to the designer to determine if the design requirements have been adequately met. This is the same data as in the Design Results form.
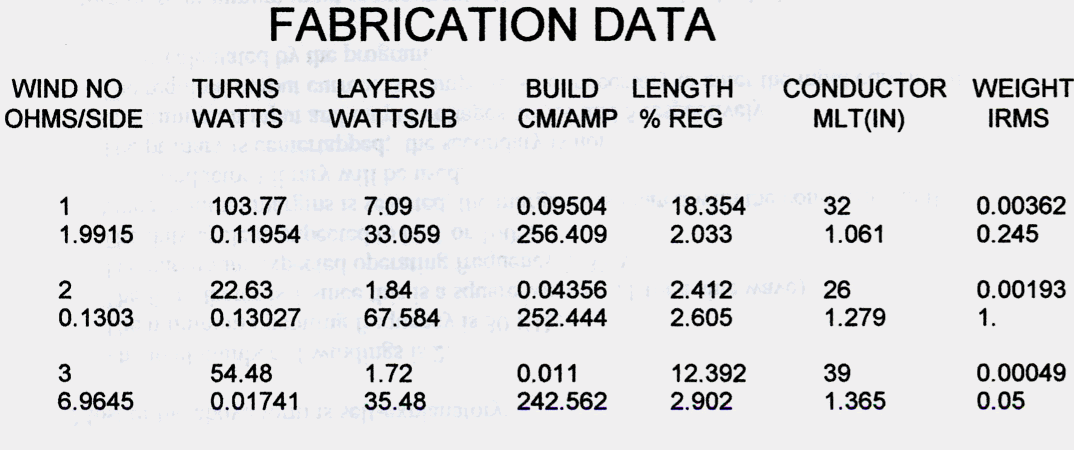
The Fabrication Data printout shows data needed by the shop to fabricate the transformer. This is the same data as is available in the Fabrication Results form.
The design can now be:
- 1. Sent to the shop for fabrication.
- 2. Saved for future reference.
- 3. Modified using the manual design techniques described in the online manual and recalculated.
- 4. Printed. In addition to the above-described printouts, any of the design forms can be printed.
Manual Design (without the AutoDesign feature):
Start TRANSFORMER DESIGNER from the Start menu
- Click "Start" then "Diogenes" then "TRANSFORMER DESIGNER".
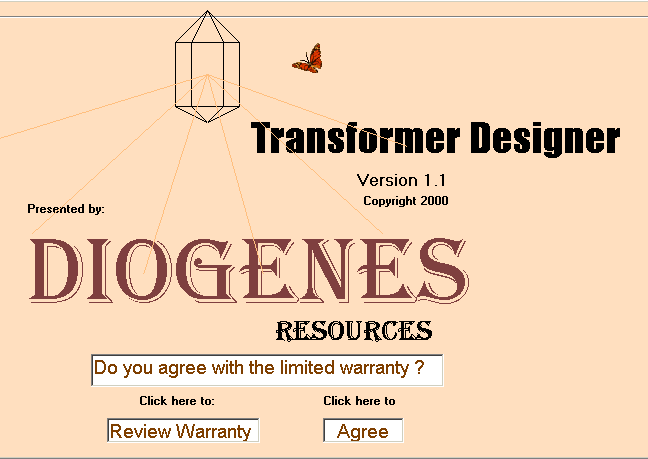
The first ("Splash") screen gives you an opportunity to review the limited warranty (click the "Review Warranty" box). After reviewing, click the "Agree" box to continue. The main screen will then appear.
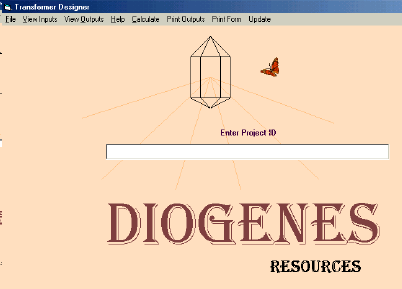
Familiarization:
The easiest way to become familiar with the program is to load an example project. You may want to stick to the large type in this manual the first time through to get the flavor of the program. Load NH60TRY1.dio from the Sample Programs by clicking on the "File" menu then "Open" then navigate to the CD and open NH60TRY1.dio.
After loading, several forms are available for viewing. Click on the view menus (View Inputs and View Outputs) to view the forms available. Notice that the input forms have been completed (Core Entry Data, Winding Data Entry, and Display Conductor Constants). If you begin a new design, most of this requires completion by the designer (with help of the optional libraries), but in this case , the design has been entered earlier and saved. The output forms are still blank and will be completed by the computer (Display Design Results and Display Fabrication Results). This program saves all the input data but none of the output data.
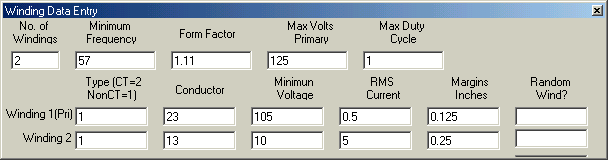
Perusal of the Winding Data Entry form reveals the output (Winding No. 2) is 5 Amps at 10 Volts or about 50 Watts and the input volts and amps are consistent with this. Also, there are two non-center-tapped windings, the min frequency is 57 Hz, the waveform is sine wave ( since the Form Factor is 1.11), the max input V is 125V and the max duty cycle is unity (per unit).
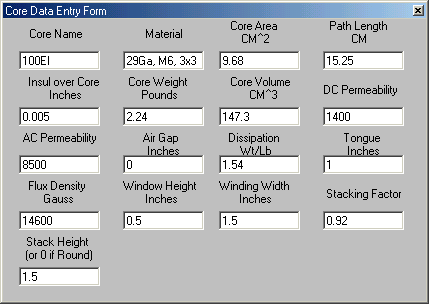
From the Core Entry form, we see the core is a non-square (1.5 per unit) stack of 100EI M6 29Ga with a stacking factor of 0.92. The insulation over the core is 5 mils, the AC Permeability is 8500 (core material only, program adjusts for air gap), the DC Perm is 1400 (core material only, program adjusts for air gap), the maximum allowed flux density is 14.6 Kg and the power dissipation is 1.54 Watts per Pound of core. The rest of the inputs describe core physical characteristics.
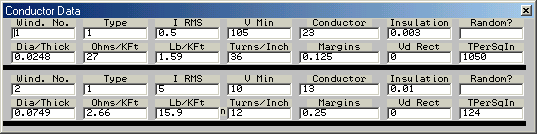
Clicking on Display Conductor Constants from the View Inputs menu results in a form which contains the parameters of the winding conductors. Some of this automatically appears from earlier entries, but diameter or thickness, the pounds/KFt, the Ohms/Kft, the turns/inch, and the diode drop (zero if no diode is in the winding) must be entered (with the help of the Conductor Library, which is discussed later).
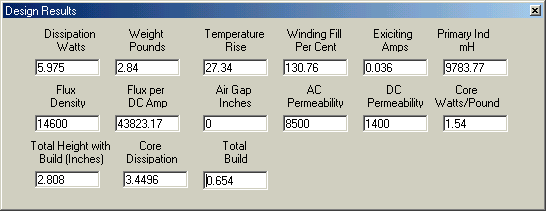
After all these entries are complete, click on the Calculate menu. The results of the calculation are immediately available in the Design Results form. This form shows the build is too high (130%) so that the core could not be stacked. The temperature rise is low (27degrees C) which suggests that smaller wire or more turns could be used. The exciting current is low (.036 Amps or 7.2% of the 0.5A primary current), presenting no problem. The flux density per DC Amp is quite high, suggesting that very little unbalance in the circuit could be tolerated, but this is a sine wave transformer and presumably has no unbalance.
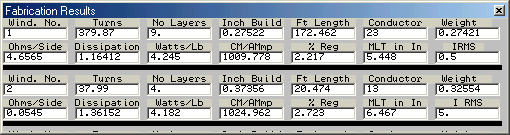
The Fabrication Results form, available for viewing from the View Outputs menu, shows the primary turns to be 380 and the secondary turns to be 38.
A lot of the information on the Fabrications Results form is useful when actually fabricating the component: the build, length of conductor, weight, and MLT of each winding. Other information is useful for the designer in optimizing the design: build, ohms/side, dissipation, watts/pound, CM/A (circular mils/Amp), and % regulation for each winding.
The only real problem with this transformer appears to be the excessive build. One possible way to reduce the build is to reduce the margins of the windings. This can be accomplished on the Winding Data Entry form merely by changing the margins to zero. Also, changing the max allowable flux density on the Core Data Entry form to be 14700 G instead of 14600 G can reduce the turns slightly. This can be done on the present forms or NH60TRY2.DIO can be loaded, which already includes these changes. After recalculation without margins, it is seen that the % winding fill is reduced from 130% to 100%. This calculation includes a 10% bulge factor, which is probably enough for most situations, but experience with the actual shop results at a particular company may require a more conservative number. Since I would not feel safe with this number, and the temperature rise is low, suggesting that the design is too conservative, another calculation is in order. The primary winding wire size was reduced from #23 to #25 (same as NH60TRY3.DIO).
If the optional Conductor Library has been authorized, the reduction in wire size can be accomplished in various ways. In the Winding Data Entry form, click on the name of conductor No. 1, which is "23". This causes "Focus" to be acquired by that entry box. Click on the next box (or anywhere else), causing the Conductor name box to lose focus and an Action menu is displayed with several alternatives to entering the data for that particular winding:
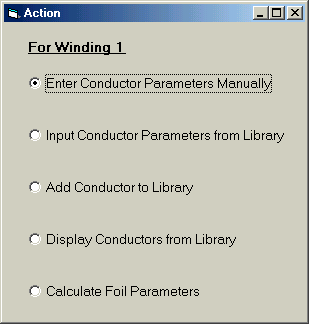
If you merely close the Action form or if you select "Enter Conductor Parameters Manually", or do nothing with it, no changes are made.
If you select "Input Conductor Parameters from Library", the program searches the Core Library for whatever conductor name is in the entry box at that time. If the conductor is found, the values from the Library are entered on the form. If the conductor is not found, no changes are made, and you are notified that the conductor is not in the Library.
If you select "Add Conductor to Library", all the data for that winding is entered in the Library. The Conductor Library is then opened, revealing the data from the table which will be saved under that conductor designation. You then have the opportunity to add additional information that may be useful to you but not required by the program. If a conductor with that name is already in the Library, you will receive a message to that effect, and you will be required to delete the previous record before you can enter the new record. Or you could modify one of the names.
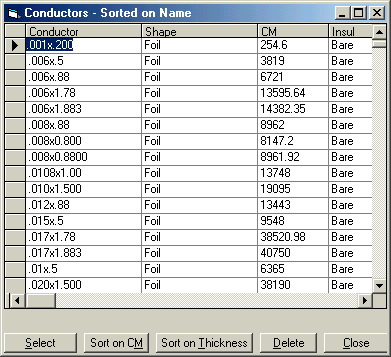
If you choose "Display Conductors from the Library", the Conductor Library opens, sorted by conductor name. The window can be maximized for easier reading. You can then peruse the Library, Add data and conductors, Delete conductors, or Select a conductor. If you select a conductor, the data for that conductor will be entered on the Winding Data Entry form for the conductor name which lost "Focus". While the Library is displayed, you also have the option of resorting by Thickness or CM (circular mils), which can be useful when optimizing windings.
The last option calculates the parameters for a foil conductor. Enter the dimensions you require (i.e., .002x.500) and the program will calculate the design parameters (ohms/Kft, etc.) and enter them in the Winding Data Entry form and the Conductor Library.
The change in wire size results in about 87% winding fill (which looks about right to me) but the temp rise is still only 31 degrees C (still too conservative). (Note that the margins on winding 1 is zero for this calculation. If the conductor parameters are entered from the Conductor Library, a suggested margin of 0.125 is automatically entered, and must be changed to zero to agree with these results.) Next, the stack height was reduced to a square stack (same as NH60TRY4.DIO). Note that when the stack height is changed, the Core Area, Core Volume, and Core Weight also must be adjusted.
If the optional Core Library has been authorized, there are several options for entering core parameters. On the Core Data Entry form, set the Focus on Material and then shift it to the next box (or anywhere else). An Action form is displayed with several alternatives.
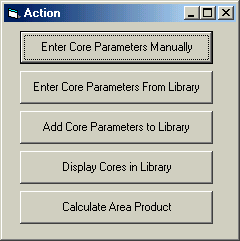
If the Action form is merely closed, no changes occur.
If Enter Core Parameters Manually is selected, the remainder of the entry boxes on the form are cleared.
If Enter Core Parameters from Library is selected, the data from the Library corresponding to whatever core name is currently displayed is entered on the Core Data Entry form. If the core is not found, no changes are made, and you are notified that the core is not in the Library.
If you select "Add Core to Library", all the data for that core is entered in the Library. The Core Library is then opened, revealing the data from the table which will be saved under that conductor designation. You then have the opportunity to add additional information which may be useful to you but not required by the program. If a core with that name is already in the Library, you will receive a message to that effect, and you will be required to delete the previous record before you can enter the new record. Or you could modify one of the names.
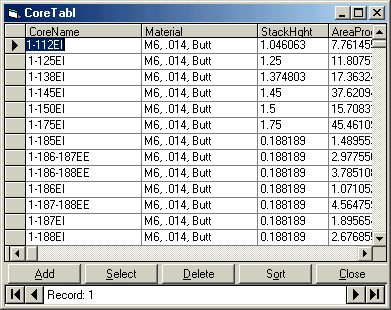
If you choose "Display Cores from the Library", the Core Library opens, sorted by core name. The window can be maximized for easier reading. The Library contains over 600 cores, selected to offer a cross-section of the thousands of cores available. Silicon iron laminations, ferrite pot, EI and U cores, and oriented silicon iron C cores are represented.
You can then peruse the Library, Add data and cores, Delete cores, or Select a core. If you select a core, the data for that core will be entered on the Core Data Entry form. While the Library is displayed, you also have the option of opening the Sort form.
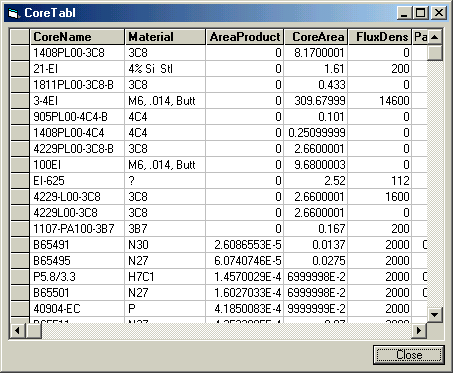
The Core Sort form allows sorting on any column (AreaProduct, CoreArea, etc.) by merely double clicking on the column header. In addition, columns can be rearranged in any order to facilitate comparisons (click and hold on a column heading while it is moved).
The final selection is Calculate Area Product, which adds the Area Product to the Core Library. The program does not use the Area Product, but the designer will find it useful when comparing cores.
Reducing the stack height caused the fill to rise to 121% and the temp rise to increase to 35 degrees C. Since the temp rise is still moderate, the wire size on the secondary was reduced from #13 to #17 (same as NH60TRY5.DIO )(Note that if #17 conductor parameters are entered from the Conductor Library, the suggested insulation is .007 inch versus the .010 in NH60TRY5.DIO, producing slightly different results). Note that the secondary winding was chosen because the watts/pound was low and the CM/amp were high for this winding as seen on the Fabricate Results form. The result is an acceptable (to me) fill of 85% and a marginal temp rise of 53 degrees C. This temp rise is probably acceptable in most cases, but if it is not, a slight increase in stack height could probably effect a compromise.
The above illustrates the methods and uses of some of the data calculated. A designer would probably review some of the values originally estimated: AC & DC permeabilities, core watts/pound, maximum flux density, etc., to ensure that they are still consistent with the final operating conditions.
Some of the parameters calculated by the program which are usually not available to designers, such as flux/DC amp, number of layers (with fractions), length of conductor, weight of each winding, CM/amp, %reg of each winding, and watts/pound of each winding can be valuable at times in determining which method of optimization to employ.
Printing Data:
From the Print Outputs menu, you can print the Design Data or Fab Data. Also, from the Print Form menu, you can print any of the program forms, including the main form. The current data is printed with the form.
Saving Designs:
Any design can be saved with the Save or Save As commands whether complete or not. Only the inputs are saved - the outputs must be recalculated from the inputs. Almost all the input data (including the project name, which appears in the center of the Main form) can be changed at any time - just enter new data and save.
New Designs:
For a new design, click on New from the File menu. The program prompts for a project name for the design and clears all the forms to blank. All the input data must then be entered before calculation is enabled. However, the design data can be saved at any time, it does not have to be complete. The partial data can be retrieved and completed later. Also, a previous design which is similar can be loaded and modified to meet the present requirements to save input time.
Sample Designs:
To illustrate some of the flexibility of the program, several sample designs are included on the CD in the Nsamples directory (files with the .dio extension). Most of these files were developed with the AutoDesign feature. There are U-Cores and Pot Cores, a design with eight windings, round wire, litz wire, and copper strip conductor and one with fairly high power. Most are high frequency square-wave designs. These samples are intended to illustrate some of the possibilities and do not pretend to be finished practical designs.
Installation
Close any open applications, especially any virus software or security programs.
Put the Transformer Designer CD in a disk drive and type D:Setup at the Run command. (“D” is your CD disk drive). For Windows NT, it is also required to run KEYSETUP.EXE, which is resident on the CD (requires “Administrator”permission). The suggested locations for files are recommended. Keep “Newer Files” if asked. If a registering error occurs, click “Ignore” and continue the installation. It is necessary to copy Conductors.mdb and Core.mdb from D:\Support to C:\Program Files\TransDes\, which must be created if it is not available (unless the libraries have been customized, and it is not desired to revert to the original libraries). If access to the sample designs is desirable, the contents of D:\NSamples\ should also be copied to the same directory (or any other convenient directory).
If an error is encountered requiring file updates before installation can proceed, the following procedure can be used:
Quit the setup procedure. Run Project28F.exe from the CD. Copy Conductors.mdb and Core.mdb to C:\Program Files\TransDes\, which must be created if it is not available (unless the libraries have been customized, and it is not desired to revert to the original libraries). If access to the sample designs is desirable, the contents of D:\Nsamples\ should also be copied to the same directory (or any other convenient directory
Windows 95: Transformer Designer is not recommended for operation with Windows 95 because some of the fonts are nearly illegible. However, Microsoft support informs me that CDOM95.EXE must be executed before installing Transformer Designer in order for the Core and Conductor libraries to be accessible. It can be downloaded from the Microsoft COM web site.
Windows 98: Transformer Designer is compatible with Windows 98 if DCOM98.EXE is executed before installing Transformer Designer (in order for the Core and Conductor libraries to be accessible). DCOM98 can be downloaded from the Microsoft COM web site.
Transformer Designer should be compatible with Windows ME, XP , NT , Vista and 2000 without special considerations.
Installing the Security Device:
The security device (“dongle”) must be connected for the program to function properly.
If a USB dongle is furnished, don’t install the dongle until after running the installation program. Run INSTALL.EXE from the Security Folder on the CD. Pick USB when questioned and click INSTALL. Then, when prompted, attach the USB dongle and let the Windows Installation Wizard run. (If the Installation Wizard doesn’t start, click START, CONTROL PANEL, and ADD HARDWARE.
If a parallel dongle is furnished, the computer should be powered down before installing the security device. Printers or other devices can then be connected to the security device. Run INSTALL.EXE from the CD.
Uninstalling:
Uninstall with the usual Windows utilities. It is recommended to keep any shared files for which there is a choice.
Installing the Security Device:
The security device (“dongle”) must be connected for the program to function properly.
If a USB dongle is furnished, don’t install the dongle until after running the installation program. Run INSTALL.EXE from the Security Folder on the CD. Pick USB when questioned and click INSTALL. Then, when prompted, attach the USB dongle and let the Windows Installation Wizard run. (If the Installation Wizard doesn’t start, click START, CONTROL PANEL, and ADD HARDWARE.
If a parallel dongle is furnished, the computer should be powered down before installing the security device. Printers or other devices can then be connected to the security device. Run INSTALL.EXE from the CD.
Uninstalling:
Uninstall with the usual Windows utilities. It is recommended to keep any shared files for which there is a choice.
Parameter Descriptions:
Core Data Entry Form:
The Core Input form contains the core data which is designated by the designer. Descriptions of the parameters follow:
Core Name: Description of Core (Text)
Core Material: Material of Core (Text)
Core Area: Cross-sectional area of core in square cm
Path Length: Length of magnetic path in cm
Insulation Over Core: Insulation over core or bobbin in inches
Core Weight: Weight of core in pounds
Core Volume: Volume of core in cubic cm
DC Permeability: Permeability to DC under the prevailing conditions (Core material only - the program adjusts for air gap)
AC Permeability: Permeability to AC under the prevailing conditions (core material only - the program adjusts for air gap)
Air Gap: Air Gap in Inches
Dissipation Wt/Lb: Power dissipation in the core in Watts/Pound under prevailing conditions
Tongue: Width of the tongue for Laminations or square cores or the diameter of the core for round cores. If there is a bobbin, use bobbin dimensions (Inches)
Flux Density: Maximum AC flux density allowed in Gauss. Used to determine the number of turns required.
Window Height: Height of the window in inches. If a bobbin is used, reduce the window height accordingly.
Window Width: Width of the window or bobbin if used in inches
Stacking Factor: For laminated cores, use the manufacturer’s recommendations. For solid cores, use unity
Stack Height: For laminated cores, this can vary. Also, solid rectangular cores could be stacked double or triple. For round cores enter zero.(inches)
Winding Data Entry Form:
The Winding Input form contains some of the circuit parameters and specifies the winding conductors.
No. of Windings: The total number of windings on the component, including the primary (drive) winding
Minimum Frequency: The minimum operating frequency. This will be used to establish the maximum flux density. (hertz)
Form Factor: This is the ratio of the RMS current value to the average current value. (1.11 for a sine wave, 1 for a square wave, 1.73 for a triangle wave)
Max. Volts Primary: This is the maximum (RMS) primary voltage. This is used to calculate the maximum flux density, not for turns ratio calculations.
Maximum Duty Cycle: This is the maximum duty cycle that will occur per unit of the half cycle.
Type: Use 2 for center-tapped windings and unity for non-CT windings.
Conductor: Description of the conductor. Can be round, square,
Minimum Voltage: The minimum voltage for each winding. Will be used to determine turns ratios.
RMS Current: Maximum RMS current expected in the winding.
Margin: Margins at each edge of the winding, specified in inches
Random Wind? Anything beginning with a "y" or "Y" will cause the program to calculate a random wound winding. Anything else will designate a layer winding.
Display Conductor Data Form:
Some of the constants for this form will be entered by the previous forms, but the rest must be entered before a calculation is possible. These parameters are mostly general characteristics of the conductors.
Wind. No.: The windings are numbered by the program, starting with the primary.
Insulation: This is insulation between layers or over the associated winding in inches
Dia/Thick: This is the overall diameter of a round wire or the thickness of a rectangular or strip conductor.
Ohms/Kft: Ohms per thousand feet of conductor at the expected operating temperature (assumed to be 100 degrees C in the Conductor Library
Lb/Kft: Pounds per thousand feet of conductor.
Turns/Inch: Turns per linear inch of winding for this particular conductor.
Vd Rect: Expected voltage drop of the rectifier in the circuit associated with the winding, if any (zero for no rectifier).
Display Design Results Form:
The parameters calculated and presented here are useful in determining if a problem is evident in the design and help determine possible changes to effect improvement.
Dissipation: Total component power dissipation in Watts.
Weight: Total component weight in pounds.
Temperature Rise: Temperature rise in degrees Centigrade above ambient. This is an empirical calculation based on weight.
Winding Fill: The percent of the available window height that is filled, assuming a 10% bulge factor.
Exciting Amps: Approximate exciting current in amps at the operating frequency with the maximum operating voltage and the calculated primary inductance.
Primary Inductance: Calculated primary inductance in mH.
Flux Density: AC flux density that was entered by the designer on the Core Input form.
Flux per DC Amp: The calculated flux density that will result from each Amp of DC current (or DC unbalance) in the primary winding.
Air Gap: Air gap in inches that was entered by the designer on the Core Input form.
AC Permeability: AC permeability that was entered by the designer on the Core Input form.
DC Permeability: DC permeability that was entered by the designer on the Core Input form.
Core Watts/Pound: Core dissipation in Watts/pound that was entered by the designer on the Core Input form.
Total Height w/Build: Total height of an EI or other shape, consisting of the stack height plus twice the build. Meaningless for Pot Cores.
Core Dissipation: Power dissipation in the core alone, one component of the total dissipation.
Total Build: Total accumulated build of all windings
Fabrication Results Form:
The Fab Results form lists entered and calculated data which is useful mainly in manufacturing. However, some of the parameters can be valuable to the designer when optimizing the design.
Wind. No. The winding number is assigned by the program, starting with the primary.
Turns: Calculated turns of each winding.
No. Layers: Number of layers for each winding.
Inch Build: Build of each separate winding, in inches.
Ft. Length: Length of wire for each individual winding in feet.
Conductor: Conductor description entered by the designer on Winding Input form.
Weight: Individual winding weight.
Ohms/Side: Resistance of one side of a center-tapped winding or end-to-end of a non-center-tapped winding.
Dissipation: Individual winding power dissipation in watts.
Watts/Pound: Calculated dissipation of each winding divided by the winding weight to aid decisions about which winding to change.
CM/Amp: Circular mills of cross-section of each winding conductor divided by the current in the conductor to aid in decisions about which winding to change.
% Reg: Percent regulation of each individual winding. Useful for circuit design and power distribution purposes.
MLT in In: Mean length of turn for each individual winding in inches.
I RMS: RMS current in each individual winding entered by the designer on the Winding Input form.